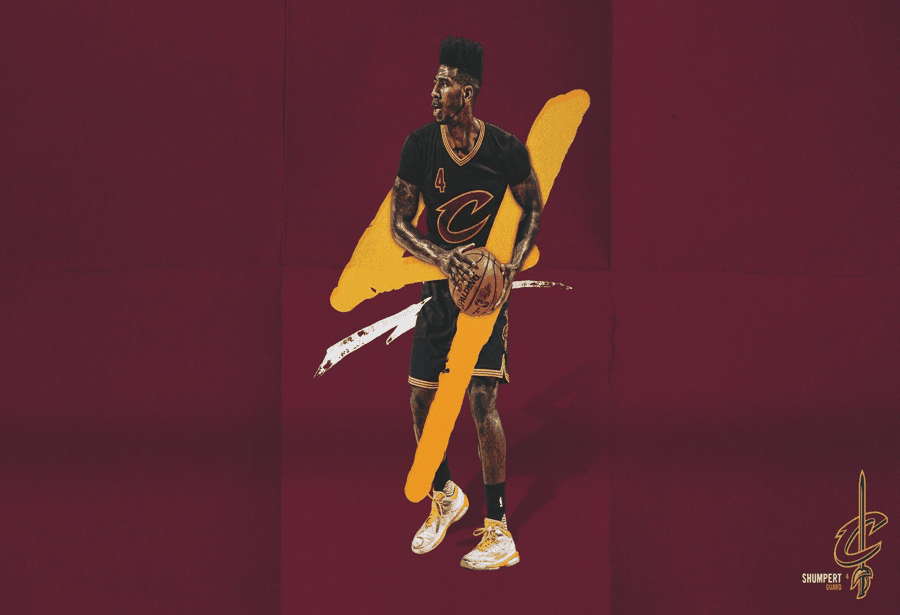
我們在切削金屬時
,刀具一方麵切下切屑
,另一方麵刀具本身也會逐漸磨損並鈍化
。刀具磨損到一定程度
,就需要換刀或更換新的 刀刃
,才能進行正常切削
。
因為刀具磨損後
,使工件加工精度降低
,表麵粗糙度增大
,並導致切削力和切削溫度增加
,甚至產生振動
,不能繼續正常切削
。因而刀具磨損直接影響加工效率
、工件質量和成本
。
刀具的磨損是不可避免的
,但是我們可以采取一定的措施使刀具的磨損減少
。
刀具的磨損主要有粘蝕
、擴散
、塑性變形
、疲勞破壞
、粘屑剝落、機械擦傷
、化學磨損等
。它們形成的原因各不相同
,下麵小編就造成這幾種磨損的原因及減少磨損的措施探討如下
:
1
、粘蝕
原因
:在低速或中速切削過程中
,由於刀具的晶粒被工件材料粘結而與母體分離
,從而在磨損麵上出現微觀凹坑
。影響粘蝕的主要原因有
:刀具表麵層的狀態及組織
,接觸麵間粘結牢固程度
。
針對以上原因
,可以采取以下措施減少粘蝕磨損
:
①提高切削速度使運動平穩
,減少振動
,避開積屑瘤的不穩定區域
。
②使用潤滑性能好的切削液
。
③改善工件材料加工性
,使在接觸麵上形成保護層等
。
2
、擴散
擴散是指在高速切削時高溫下活性原子由於濃度差而形成的擴散
,其具體表現為有擴散層
,微觀較平
。影響擴散的因素有: 接觸麵的溫度
、元素相互擴散速度
、切削時相對運動速度等
。
針對以上原因可以采用以下措施減輕磨損
:
①選擇元素相互擴散速度較低的刀具材料
。
②在硬質合金表麵塗履TiC,TiN, Al 2 O 3 等
。
③避免過高的切削速度
。
④由工件材料在接觸麵上形成保護層
。
3
、塑性變形
塑性變形主要體現在大切削用量切削
,或者切削難切削材料時
,由於刀具受到的負荷超過在切削區高溫下的刀具材料屈服強度而使刀具組織塑性流動而纖維化
,其主要影響因素有
:工件材料的強度
、刀具材料高溫抗屈服強度、進給量
、切削速度等
。使用高速鋼刀具時的塑性變形比硬質合金嚴重
。
針對以上原因可以采用以下措施減輕塑性變形
:
①避免大的進給量與切削速度
。
②刃口強化
,選擇刀尖圓弧半徑Ra 合理的數值
。
③提高冷卻效果
。
4
、疲勞破壞、粘屑剝落
疲勞破壞
、粘屑剝落是指在斷續切削時
,當機械應力與熱應力超過刀具疲勞強度
,粘在前刀麵上的切屑第二次切入時因衝擊造成剝落主要表現為刀具出現裂紋
、剝落
、崩 刃等
。這種磨損較為嚴重
,影響這種磨損的主要因素有
:機械應力與熱應力交變的頻率與大小
、刀具材料的疲勞強度
、粘屑的牢固程度等
。
針對以上原因可以采用以下措施來減輕這種磨損
:
①在高速切削時
,使用熱膨脹係數低
、導熱係數高的刀具材料
,避免過高的切削速度
。
②在低速切削時
,減少進給量
。
③在車
、刨時
,采用大的負刃傾角
。
④適當減少後角
,在刀刃上磨出負倒棱
,將刃口研磨成一定的圓弧半徑。
5
、化學磨損
在使用各種不同的切削液或氣體時
,可能會出現機械擦傷
,我們把這種機械擦傷叫化學磨損
。其主要原因是
:因氧化作用而降低強度或與極壓添加劑作用而降低強度
,當采用適當控製極壓添加劑的含量
,或選用化學穩定性好的刀具材料時可以減少這種磨損
。
以上列出了幾種磨損的原因及預防措施
,但必須指出的是它們之間還有相互的影響
,對於不同的刀具材料
,在不同的切削條件下
,加工不同工件材料時
,其主要磨損原因可能屬於其中的一種或幾種
。一般說來
,對一定的刀具和工件材料
,對磨損起主導作用的是切削溫度
,在低溫區通常以機械磨損為主
,而在較高溫區
,則往往以粘蝕
、擴散、化學磨損為主
。隻有當我們找到了刀具磨損的主要原因
,才能采取相應的措施
。